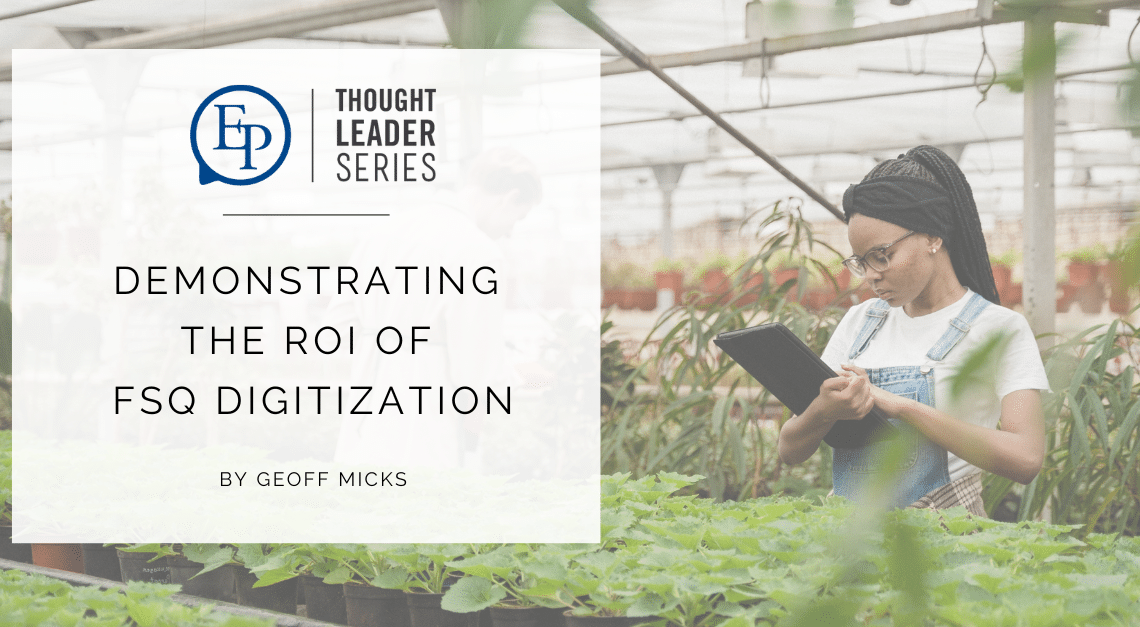
One of the great challenges of Food Safety and Quality professionals is connecting what they do to the bottom line of the company, especially when they are advocating for new tools and capabilities.
We have discussed this briefly before in an earlier blog post. While FSQ is vital to the success of every business that works with food, it is not a profit generator or a competitive advantage. There is also a natural and deep-seated conservatism in tinkering with what already works among the people responsible for safeguarding what we eat and drink.
All this adds up to it being very difficult to fit Food Safety and Quality into the normal conversations we have about Digital Transformation.
Executive Platforms has successful summit series dedicated to gathering the senior leadership responsible for Human Resources, Finance, Sustainability, Technology, Manufacturing, Pharmaceutical and Biopharmaceutical Manufacturing, and North American and European Supply Chains, and in all those programs, the Digital Revolution is heavily featured with lots of real-world case studies and clear demonstrations of major changes in productivity and effectiveness.
Our Food Safety & Quality event has some of that content too, but it is often merged into larger conversations around supply chain and supplier management, risk management, or Safety and Quality Culture, or automating some of the documentation necessary for regulatory compliance. It’s not that digitization isn’t involved, but it doesn’t get the starring role it enjoys in so many of our other agendas.
For today’s column we want to explore the Digital Revolution in the FSQ space, and connect the resources committed to change to tangible improvements that demonstrate a return on the investment of the time, money, hardware, software, and people needed to make a digital transformation a success.
Where Do We Start?
As we have discussed in our earlier conversation around successful digital transformations, the first step is to set clear and realistic goals for what you want to do. While that might sound obvious, you would be surprised how many digital transformations fail to meet expectations because they were unfocused and hazy on just what was supposed to be achieved in the first place.
So what does the Digital Revolution offer the FSQ professional? What are some clear and realistic goals that new tools and capabilities would allow them to achieve better than ever before?
Compliance might be an interesting place to start. FSMA and HACCP both are asking Food Safety and Quality professionals to document, record, and analyze their work in a way that was not the industry standard before. If one of the pushbacks against modernization is, ‘If it’s not broke, don’t fix it,’ here we have a great place where things have changed —something new has happened— there is no ‘the way it has always been done,’ and the people who are trying to do their compliance work with clipboards, logbooks, and excel spreadsheets are finding themselves overwhelmed.
Just as we are now seeing in the Life Sciences space, automating data collection, data analytics, and data reporting is freeing up the subject matter experts from repetitive and mundane tasks to actually act on the data, to troubleshoot, to seek ways to improve processes based on what the software is flagging to the attention of a human being with the experience and knowhow to work a problem that they used to spend more of their time looking for rather than solving.
Compliance may not be a profit center, but it is vital work that must be done, and the demands of regulators and the expectations of the public are asking more and more of FSQ professionals. If there is a place where investing in digital tools is going to pay immediate and demonstrable dividends, compliance is a great starting point.
What About Workforce Challenges?
Every industry Executive Platforms deals with is experiencing high turnover in the wake of COVID-19, and this can be especially challenging for Food Safety and Quality professionals. You need motivated and knowledgeable people to do FSQ work. You also need the whole company to be an active part of Safety Culture and Quality Culture. Losing experienced employees and bringing in new people erodes the institutional knowledge and culture of continuous improvement Food Safety leaders depend on.
Here again digital tools can step in and both reduce the workload on Top Talent while also empowering frontline workers to make a larger contribution to QA/QC without time-intensive training. This podcast episode offers a great example of what we are talking about. With the right UI, every employee who works with food can be putting information into the system and taking instructions out of the system to understand what is going on at every step of the product’s journey from farm to fork. Twenty years ago the idea that the fields, the trucks, the factories, the DCs, and the grocery stores would all be sharing data on the same platform and giving it to entry-level employees to both input what they are seeing and act on the output of what the system gives them would have been science fiction. Today, it’s how companies are getting more out of their workforce without increasing headcount. That right there is an enormous ROI on putting the Industrial Internet of Things into the hands of Food Safety and Quality professionals.
Better Understanding Protects the Brand and the Public
There’s no getting around it. The Digital Revolution is built on data, and the more data it has, the more powerful a tool it offers to whoever is feeding it information. Food Safety Risk used to be about a combination of experience, intuition, and the cost-benefit analysis of a seasoned veteran as FSQ professionals look to make the best use of their resources while striking a balance between the low impact-high frequency threats and the high impact-low frequency threats. Today, all of those calculations can be determined by software much faster and to a much higher degree of accuracy than any one person or team of people can do. Some of the biggest companies in the world are already seeing enormous benefits from digitizing their Risk Management.
As long as we are talking about Risk Management, let’s also remember how important Supply Chain and Supplier Risk Management are to those conversations as well. The Digital Revolution is not just about getting data into a computer that crunches the numbers faster than a human being. It’s also about getting all the partners up and down the value chain tracking the same information as it relates to their time with the product and sharing it in real-time.
Do you know how powerful visibility, transparency, and traceability are to Food Safety and Quality professionals? While FSQ may not be a profit center, every recall it prevents and every brand-imperiling incident it averts saves the company more than just money. In a world of changing customer expectations, demonstrating both a commitment to safety and the ability to respond quickly and decisively to what is happening can define a business in the zeitgeist. Failure to do so can be devastating.
Rethinking ROI
We began today’s column talking about how other industries view Digital Transformation, and how those metrics often do not work in the FSQ space. Food Safety is not about more, faster, for less operating cost. Food Safety either performs as it needs to perform, or it fails. Failure is never an acceptable outcome, and when it does happen, the consequences are severe. No amount of money regains public trust.
So what is the real ROI of Digital Transformation in the Food Industry from a Safety and Quality perspective? New tools and enhanced capabilities pushback, reduce, mitigate, and may even eliminate the opportunities for FSQ to fail. That’s the long and the short of it. An argument cannot be made about making more money or outcompeting the competition. That is not the function of FSQ, and it should honestly make people a little uncomfortable to even think about Food Safety through that lens.
FSQ is about keeping people safe. The new generation of tools and technologies becoming available now and transforming every industry will help Food Safety and Quality leaders do their jobs better. They will understand and document their responsibilities better and act on challenges and opportunities in an even more timely matter. They will be able to communicate, collaborate, and coordinate internally and externally better than ever before. Companies will be better protected from risk, and more capable of responding to concerns when they do arise.
The bottom line may hold steady when resources are committed to FSQ, but the bottom line is less likely to dramatically shift because something went wrong. That is the real promise of the Digital Revolution to Food Safety and Food Quality. You can break down what improves where however you like, but it all adds up to the Food we eat and the beverages we drink will be safer. What business working in the industry can fail to invest in the Digital Revolution when those are the stakes?
—
Geoff Micks
Head of Content & Research
Executive Platforms
Geoff joined the industry events business as a conference producer in 2010 after four years working in print media. He has researched, planned, organized, run, and contributed to more than a hundred events across North America and Europe for senior leaders, with special emphasis on the energy, mining, manufacturing, maintenance, supply chain, human resources, pharmaceutical, food and beverage, finance, and sustainability sectors. As part of his role as Head of Content & Research, Geoff hosts Executive Platforms’ bluEPrint Podcast series as well as a blog focusing on issues relevant to Executive Platforms’ network of business leaders.
Geoff is the author of five works of historical fiction: Inca, Zulu, Beginning, Middle, and End. The New York Times and National Public Radio have interviewed him about his writing, and he wrote and narrated an animated short for Vice Media that appeared on HBO. He has a BA Honours with High Distinction from the University of Toronto specializing in Journalism with a Double Minor in History and Classical Studies, as well as Diploma in Journalism from Centennial College.