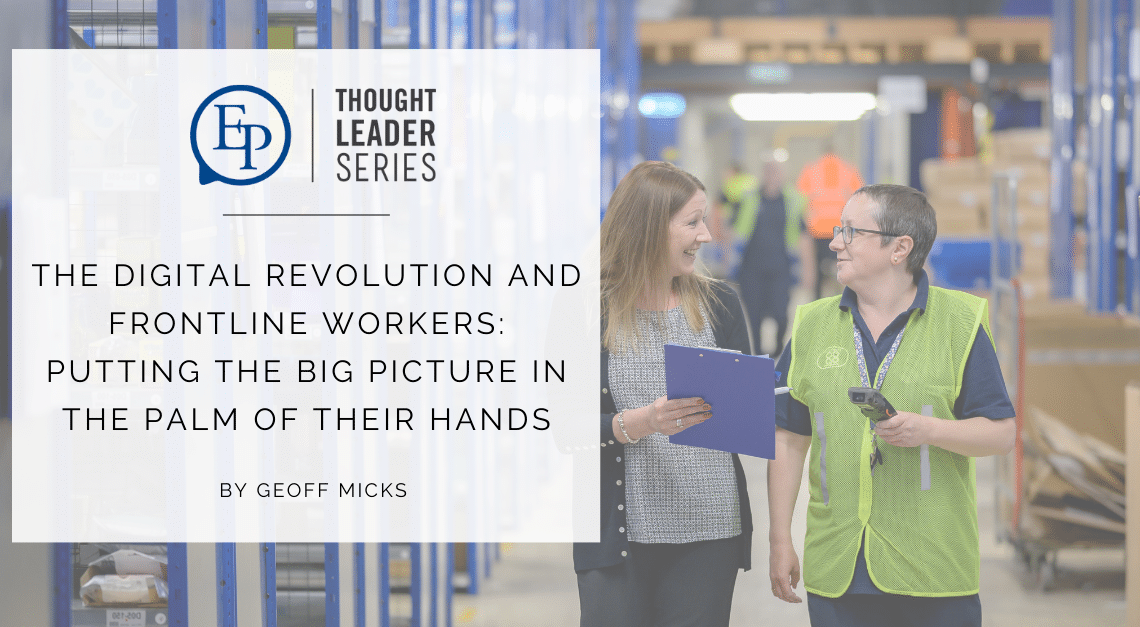
Last week marked my thirteenth anniversary as an industry conference producer, and of all the conferences, summits, forums, and symposia I have worked on over the years, the largest single category must be manufacturing events.
I love building events for people who build things.
It helps that I worked a bunch of factory jobs to pay my way through school. I crushed rock into powder. I cooked steel until it was hard enough to cut other steel. I made brake parts for trains and gas tanks for cars. When people talk about safety training or shopfloor optimization or materials handling, some part of me harkens back to my time as a young man wearing steel-toed shoes again. I feel connected to the content on the agenda in a way that is more personal and intuitive for me than some of the other subject matter I work on, even after many years.
You can imagine my surprise and delight, then, whenever I notice something new in the manufacturing space.
Now perhaps I should walk some of that back. Everything I am about to say has been discussed before. What has changed recently —dramatically changed— is how people are talking about it.
Let me illustrate what I mean with a quick story. I was in Fort Worth a couple of weeks ago at the 2023 edition of the long-running and successful North American Manufacturing Excellence Summit. I had a podcast interview scheduled with someone I have had the pleasure of speaking with several times before over the years, and as we were getting organized, I ran a few ideas by him and his comms person about how the conversation might go.
In the nicest way possible she stopped me and told her boss, “Remember: We’re not talking about Digital Transformation this year. We’re talking about people. It’s all about empowering staff.”
Now this was music to my ears. I speak about different facets of the Digital Revolution several times at each and every event Executive Platforms organizes, and one of the things I am always conscious of is that we want to talk about the people part of Digital Transformation. Things can get very ‘Big Picture,’ abstract, and technical when it is not grounded in the human beings whose working lives are being changed. Now I am being told we want to start with the people to the point where we are making a conscious effort to keep Digitization on the sidelines? They did not have to sell me on that editorial choice. I can assure you!
What’s Changed, Exactly?
While I don’t normally name names when I do quick stories like the last one, I suppose in this instance he is not going to mind, and breaking my rule lets me both say some nice things about him while also highlighting some more content and context for you.
I am talking about Willem Sundblad, the CEO and Co-Founder of Oden Technologies. I’ll update this blog with a link to our most recent interview once it’s published. He also gave a fantastic workshop presentation with a client case study at NAMES23. You can watch it here. He is also one of my favorite people to have a conversation with about Industry 4.0 topics, because he has a knack for making the complicated sound simple while illustrating what he’s talking about with great examples. This and this are great examples of what I am talking about.
When one of my go-to people for talking about Digital Transformation in Manufacturing pivots his messaging, it gets my attention. I then thought about the discussions I had already had earlier in the event, and also began asking pointed questions for the remainder of the summit, and what I kept hearing was my biggest takeaway from NAMES23.
For many years now, the Digital Revolution has been the biggest issue, trend, challenge, and opportunity facing North American manufacturers. We survey our attendees during the registration process, and we have hard data that different facets of Digitization are always top-of-mind. With that said, there is a disconnect between a manufacturing executive talking about where his or her organization is on their Digital Transformation Journey and what is happening in the day-to-day life of frontline workers. Where until very recently top-down enterprise-driven transformations were prioritized and progress was often tied to visibility and data analytics, now more and more the very real challenge of a tightening labor market is crying out for new solutions that impact the grassroots of the organization.
Illustrating the Pivot
If you want to talk about Digital Transformation today, the current business environment demands that be framed as a conversation about what it can do for frontline workers. Let’s do some before and after statements:
Before: Senior leadership wanted to talk about how much data they could collect in real-time and process quickly to understand their business better.
Now: The low-hanging fruit of Digital Transformations is less about giving executives information and more about improving productivity on the shopfloor.
That’s not a new idea, of course, but it’s where all the emphasis is going. Let’s do another one.
Before: Senior leadership worried about the quality and quantity of the data they were collecting and analyzing. The range of solutions available is daunting, and real expertise and experience often needs to come from outside the business, and so serious thought and consideration needs to go into figuring out which tools and partners are needed to get real ROI out of a Digital Transformation.
Now: The changing, tightening, turbulent labor market demands that the workforce needs technology to step up, to optimize their daily tasks, to allow one person to be more productive, and also to record how work is done well and transit those lessons to others. What is more, a workforce engaging with these tools is going to be happier in their work and see opportunities to learn and grow in their roles, which contributes to talent attraction, development, and retention.
Again, this has been a big part of any conversation about the Digital Revolution for as long as people have been digitizing manufacturing operations, but the center of gravity for where the emphasis goes has shifted dramatically. At NAMES23 I was surprised how few of the talking points I heard at NAMES20 or NAMES21 were given the spotlight. Even asking an enterprise-wide strategic question almost always produced an answer couched from how the most good any company can do right now is helping their people do better and feel better in their jobs.
Questions for Manufacturers
I have already said we talk about Digital Transformations a lot on this blog, so here are a few other links that might be helpful too. With that said, I want to get into a few prompts for manufacturing leaders who are shifting their emphasis from understanding the ‘Big Picture’ into giving frontline workers access to what they need to know to do their jobs better.
- Do you know what you want to improve? That might seem like a facetious first question, but it’s not. In the same way the enterprise-wide holistic Digital Transformations can become overwhelming simply by the number of options available to try and make it work, there are a lot of things the next generation of tools and technologies can do for the shopfloor.
- Are you looking to get better at asset lifecycle management and proactive maintenance to reduce unscheduled downtime? A lot of good can come just from knowing when a machine is going to be down for scheduled servicing while having confidence that production is not going to stop unexpectedly as a maintenance team reacts to something breaking down.
- Do you want to rethink scheduling and build flexibility into your team’s working hours? That can be a powerful tool both to improve the morale of your current employees while also giving you access to people who can’t work the traditional shift but would definitely sign up for other hours if they were made available.
- Are you looking to train people to do tasks better and gather insights into how seasoned hands and Top Talent are doing their jobs so that institutional knowledge can be retained and transmitted to others? In our new business environment of high turnover, getting people up to speed, documenting best practices, and sharing insights is going to be more important than ever.
- Are you looking to automate the boring, uncomfortable, and repetitive tasks, freeing your people up to do more interesting and valuable work? Again, in a world where people want more out of their working lives, giving them opportunities to move up and learn and do more is both a powerful retention tool, and also just good business sense to get more and higher value productivity out of the same headcount.
These are just a few ideas. Whatever you want to do with shopfloor Digital Transformation, it has to be done with purpose, and it should be something that is answering a need in the business that frontline workers are facing, not something enforced upon them from on high.
- Are you talking to the people who will be using these tools and tailoring how they work based on their input? Again, this might sound obvious when you first hear it, but it is amazing how many new tools and technologies are bought off the shelf and handed to workers with a, “You’ll figure it out” mentality. Digital Transformation should be about making their working lives easier and better. Why would a software developer have a better understanding of how to do that than the people who will be using the tool? Keep in mind…
- Are you making sure the tool is something anyone of any age is comfortable using? So many good tools don’t get used to their full potential because they are a hassle. Put some thought into the user experience and the user background. Can you make it work on an employee’s phone? If you can, can you make it simple enough for people who are ‘not good with smartphones’ to engage with it on an equal footing as people who live on their cellphones?
- Are you making sure the tool remains focused on the task at hand and what is happening each day? The only part of the ‘Big Picture’ every worker needs to understand when engaging with the tool is giving them is how they fit into it. Don’t expect a frontline worker to do any analysis beyond their existing role. The tool should be giving them enough context and instruction to do their job, and no more. Data overload and information paralysis are very real threats, but they are also very easily avoided with some conscious effort.
- Are you making sure the tool is embraced by its users, and the success of the tool is a reflection of the users’ success? The soft skills of Change Management will remain of paramount importance in all of this for it to work and build upon the benefits it brings to frontline workers. Far from a new, strange, and unwelcome addition to their working lives, this should become ‘their thing’ that ‘they use’ to do ‘their work.’ One of the best outcomes you can hope to see is when workers stop thinking of the tool as something their senior leadership imposed upon them, and start having a sense of ownership of it for themselves.
Final Thoughts
Sometimes I feel like discussions about Digital Transformation are a bit like shuffling a deck of cards. Just about any time you get into this subject, you are going to see the same talking points coming up again and again. Everyone’s story is different, of course, but they all have common elements, even if they appear in different orders. I’m two thousand words into writing about bringing the fruits of the Digital Revolution into the hands of frontline workers, and I am not saying anything I have not heard before and said before in other contexts.
What is different this time, if you will allow me to return to the deck of cards analogy, is this time it feels like the cards have been put in order, and I cannot help but deal myself out a flush or a four-of-a-kind or some other matching, winning hand. No matter which conversation I had in Fort Worth, it always ended up being about frontline workers.
The current business landscape of high turnover and the struggle to attract, develop, and retain workers has put renewed emphasis on the Digital Revolution to focus on the tactical over the strategic. I don’t know how long that will last, but when manufacturers of all shapes and sizes focus on one kind of innovation for any length of time, a lot of great ideas and real progress will come of it. I am excited to see how the promise of the Industrial Internet of Things, AI, Machine Learning, and other facets of Industry 4.0 are going to deliver new capabilities and an improved quality of working life to the rank and file employees who have always been part of the Digital Transformation journey, but rarely have held such a prominent place in the story as it unfolds.
I will be sure to talk more about this in the future, hopefully with some great illustrative examples to share.
—
Geoff Micks
Head of Content & Research
Executive Platforms
Geoff joined the industry events business as a conference producer in 2010 after four years working in print media. He has researched, planned, organized, run, and contributed to more than a hundred events across North America and Europe for senior leaders, with special emphasis on the energy, mining, manufacturing, maintenance, supply chain, human resources, pharmaceutical, food and beverage, finance, and sustainability sectors. As part of his role as Head of Content & Research, Geoff hosts Executive Platforms’ bluEPrint Podcast series as well as a blog focusing on issues relevant to Executive Platforms’ network of business leaders.
Geoff is the author of five works of historical fiction: Inca, Zulu, Beginning, Middle, and End. The New York Times and National Public Radio have interviewed him about his writing, and he wrote and narrated an animated short for Vice Media that appeared on HBO. He has a BA Honours with High Distinction from the University of Toronto specializing in Journalism with a Double Minor in History and Classical Studies, as well as Diploma in Journalism from Centennial College.